Blog
A support structure design challenge: the Danish plastic toy manufacturing and packaging plant
We have completed the construction of one of our design projects from 2020. In this post we present one of the four main buildings of the complex, a 9,000m2 packaging plant. The construction of the building started in mid-2021 and was completed in the first quarter of 2023. STUDIO IN-EX was asked to be the general designer for the construction designs and to support the construction of the buildings in the framework of a design engineer’s site supervision.
The fact that all disciplines work in the same space in our office was a great advantage during the design process, as it required constant collaboration between the design studios. Our designers all work on a common platform, a closed-BIM system, which makes their work extremely efficient. Any modifications to the structure were immediately reflected in the model, making them traceable in minutes during the design process. In all cases, the construction designs are submitted to the construction company after several rounds of clash detection in order to minimise construction errors. In addition to the 8,000m2 of packaging technology in the hall area, the main function is served by a 2×1,000sqm two-storey workshop and an office block.
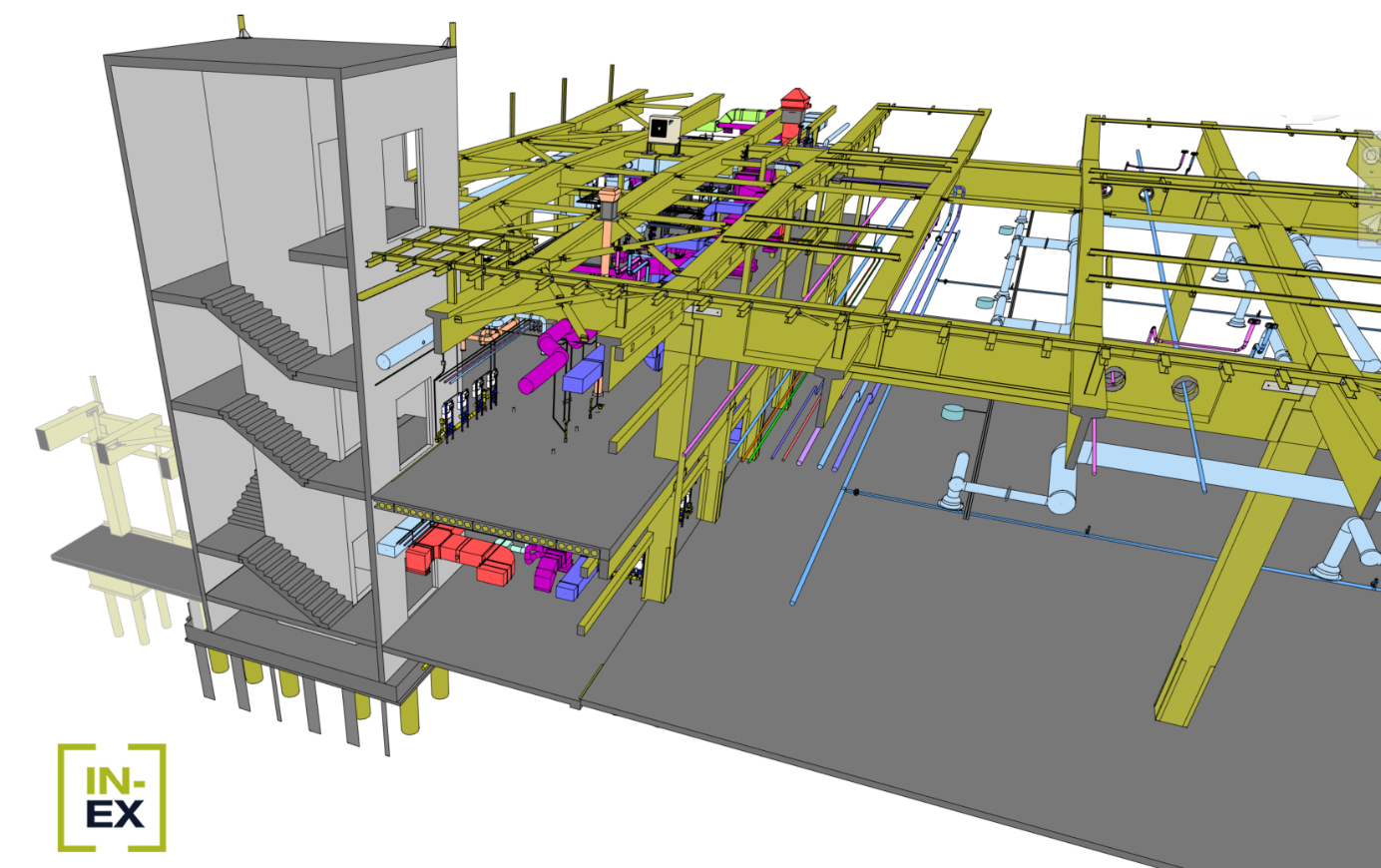
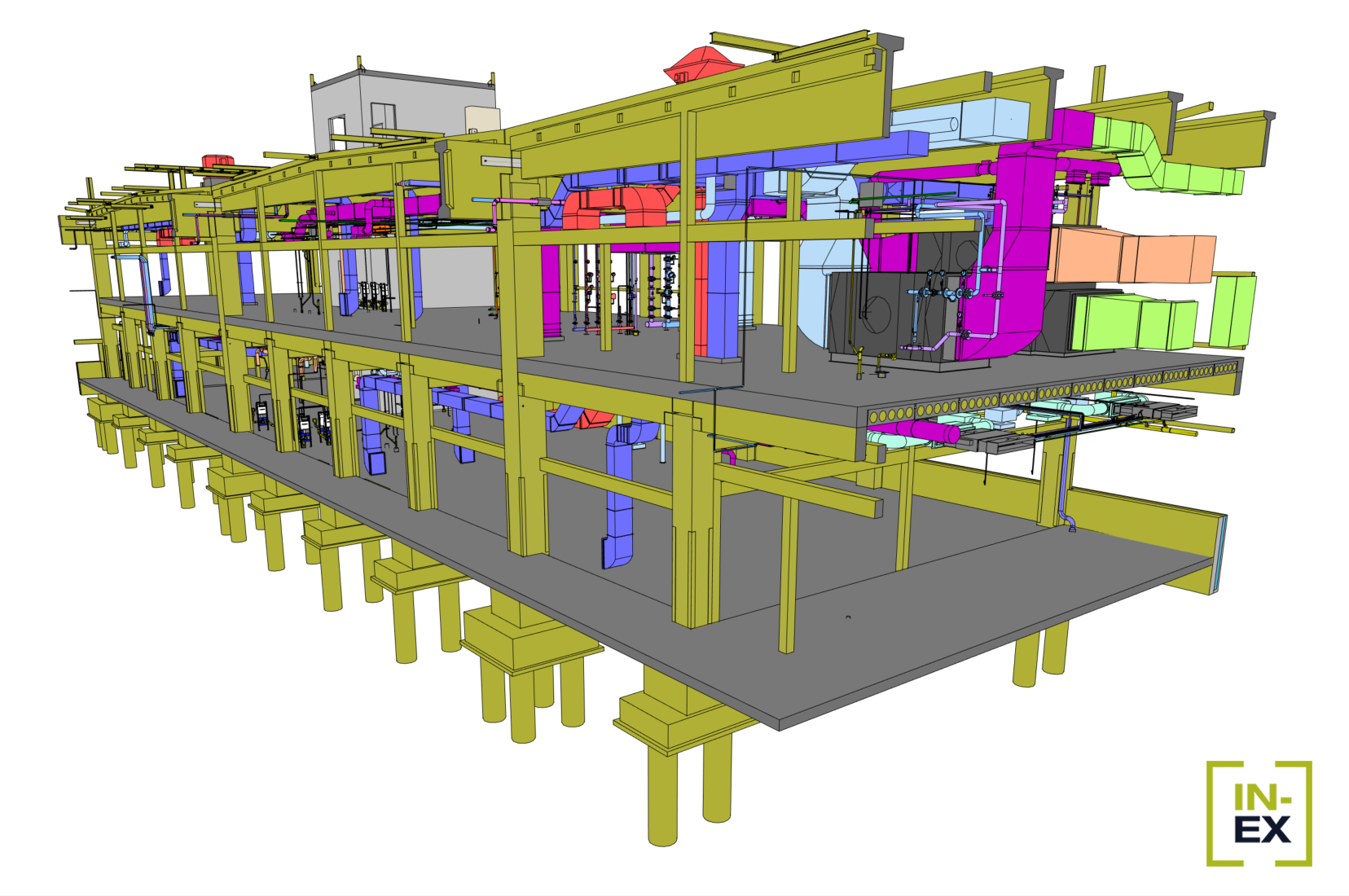
IIt was a real challenge for our structural engineers: The building is a precast reinforced concrete frame structure with pile foundations. The service headquarters was also built with a prefabricated frame slab floor consisting of hollow core slabs. The main vertical load-bearing element of the structure are the 75x75cm columns, which are supported by 120cm high prefabricated pocket necks, which also stiffen the hall in the horizontal direction. The roof structure consists of a series of 150cm high spine purlins with a span of 26.5m-23.8m-26.5m and 165cm high main beams with a span of 18.0m.
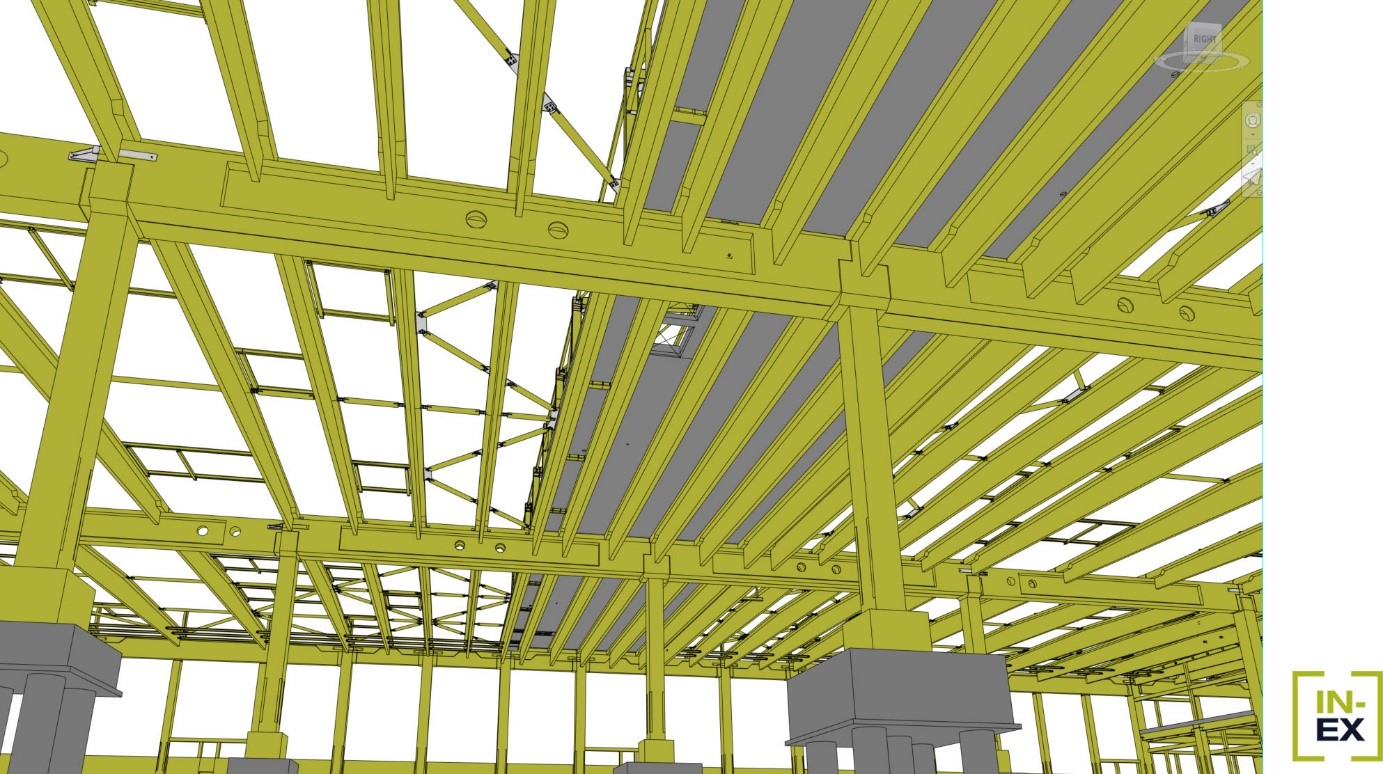
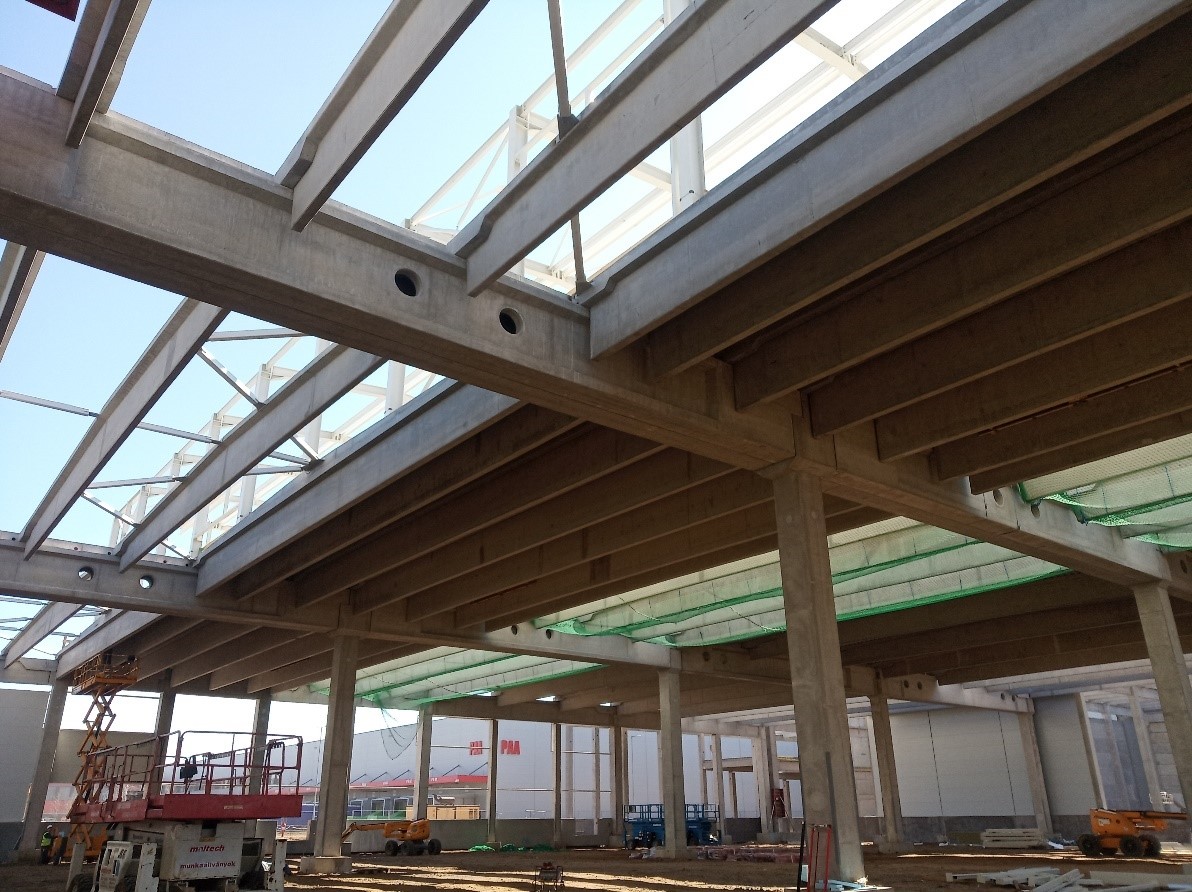
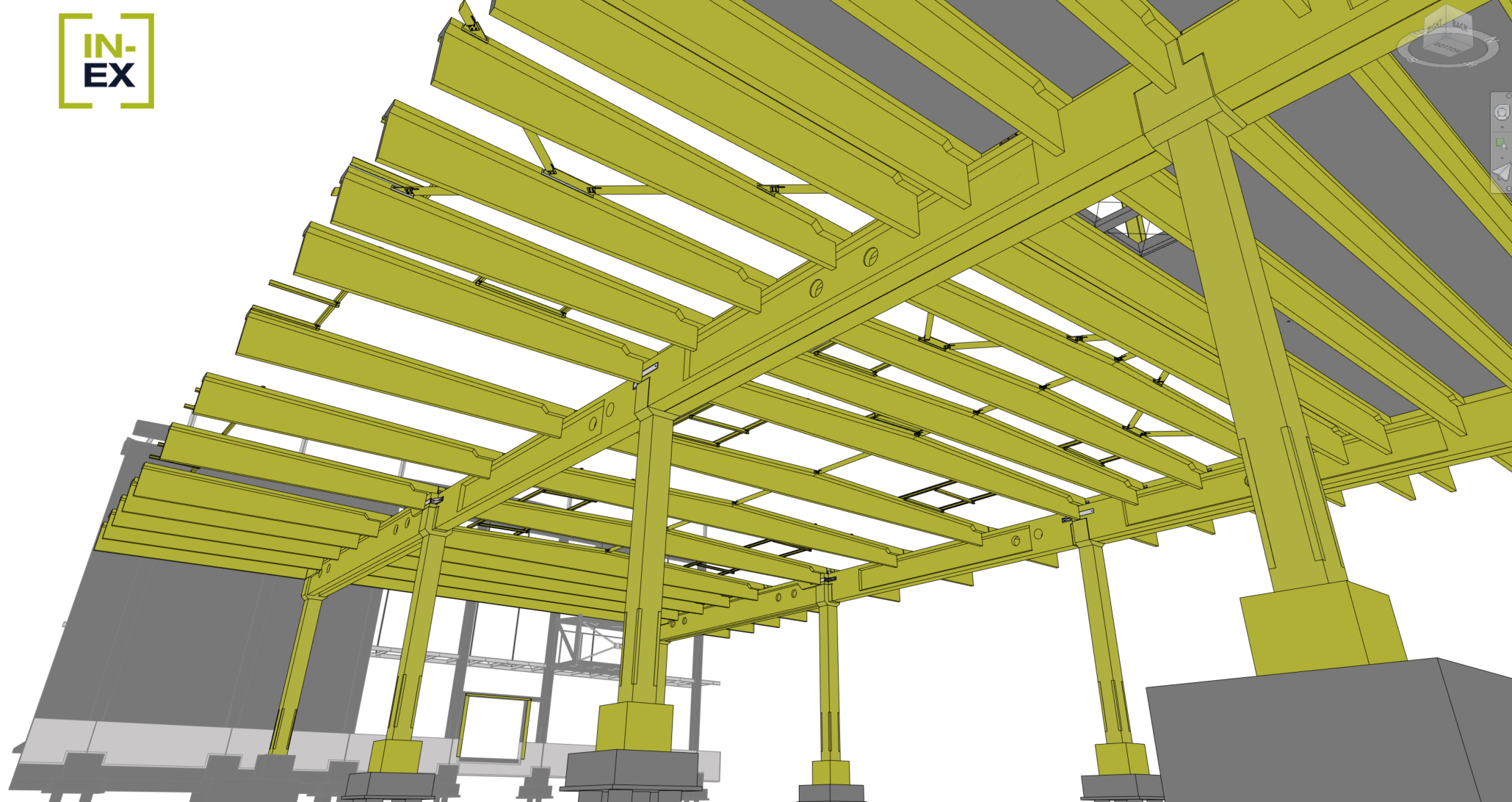
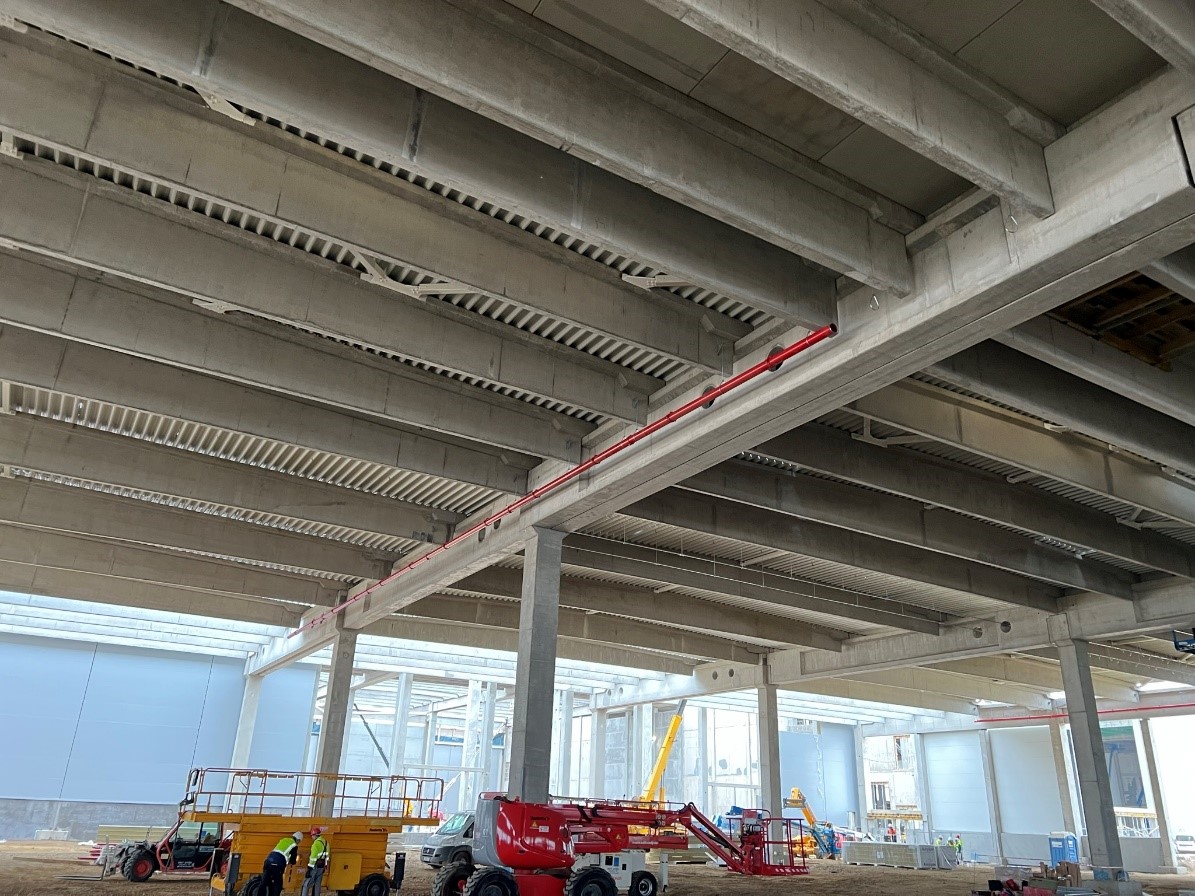
On the roof structure, 10.5m above the central section of the hall area, there is a steel-framed mechanical superstructure with a reinforced concrete slab, which houses three 9-ton air handling machines. The roof level with its superstructure and mechanical systems was subjected to significant loads, and we had to cope with the increased stresses from the earthquake during the designing.
Author: Norbert Ábelovszki, Head of the Structural Design Team
Recent posts
Final exams at the BME
Thanks to the Faculty of Civil Engineering, Zsolt Oláh was invited to be an external committee member for the MSc in MSc in Construction Information Technology Engineering to review the students' thesis and attend their final exams.
Hydro Extrusion’s solutions: heat dissipation
By Hydro's aluminium foundry project presented us with an unusual design challenge. We have strong acoustic requirements to protect the neighbourhood, and that the furnaces generate a lot of heat, which we had to dissipate while minimising noise.
Hydro Extrusion’s solutions for the support structure
In our previous posts, we introduced you to our Hydro project and the design of the casting pits that form the backbone of the technology. This time we present some exciting solutions for the support structure.
Engineering and what lies behind it
A special career orientation day has allowed students at Petőfi Sándor Gimnázium to get a glimpse of a career in engineering.
Visiting a factory building site at the beginning of your professional career
The construction of several buildings of our Nyíregyháza-based project is at such a stage that the electrical team, together with the BMS team, decided it would be worth taking a look at the work in progress.
We support the career choices of future engineers!
Since autumn 2024, our company has been an active member of the association "Together for Future Engineers" (EJMSZ).